Performance indicators of Solar Studs
The performance of a Solar Studs is measured from the following aspects.
The compressive performance of Solar Studs
If Solar Studs cannot withstand a certain amount of pressure, it will easily break after the car is crushed or impacted, and naturally cannot work normally, so compressive resistance is a basic condition for Solar Studs to work normally. But the problem is that Solar Studs itself is an electronic product that contains electronic parts. It is indeed not easy to make the electronic parts have a higher degree of compressive performance. Therefore, in general, the compressive performance of Solar Studs is better than ordinary ones. The nails are worse. As of 2014, the technical requirement of the Ministry of Communications is 10 tons.
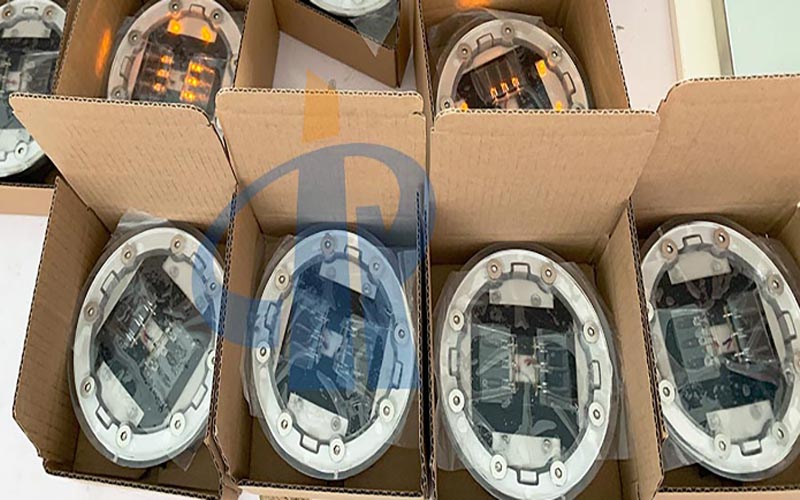
There are several ways to effectively improve the compressive performance of Solar Road Stud: One is that the exposed Solar Road Stud uses PC bulletproof materials to enhance the compressive resistance of the electronic part; the second is to use IC control as much as possible to reduce electronic circuits. To reduce the pressure on the electronic part; the third is to design some stiffeners on the shell to share the pressure on the electronic part.
sealing performance
If the Solar Road Stud is not completely sealed, it will naturally see water, which will cause a short circuit in the circuit, and the consequences are disastrous. Therefore, a qualified Solar Road Stud must pass the seal.
There are several ways to improve the sealing performance of Solar Road Stud:
(1) Separate design. The LED lampshade and the internal circuit board adopt an isolation design. Even if the LED lampshade is broken, the interior of the Solar Road Stud is still guaranteed not to seep;
(2) Adopt strong neutral bonding material to ensure that the solar panel, LED lampshade and road stud housing are tightly bonded without any gaps between them.
brightness
Solar Road Stud actively emits light and clearly outlines the road outline; compared to Reflective Studs, one of its very important features is its high luminous intensity. This indicator is required by the Ministry of Transportation to be 2000 MCD.
stability
An important factor that determines the life of Solar Road Studs is the life of the battery, and the choice of the battery is very important. There are two types of batteries on the market for reference as of 2014. One is that the battery capacity is reduced to 50% after 500 times of charging and discharging; the other is that after 1000 times of charging and discharging, the battery capacity is reduced to 79%.
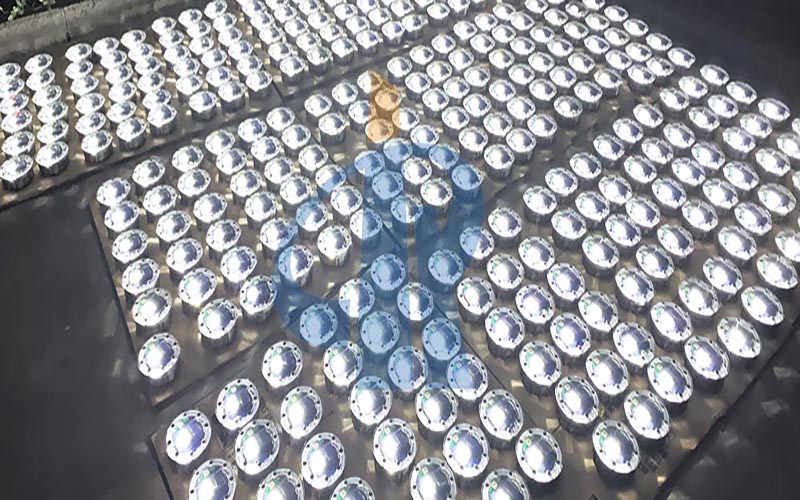
The battery life must not only be long enough, but also be able to work normally in a larger temperature range. There are chemical substances inside the battery. If the temperature is too high or too low, the battery will not work. The battery operating temperature range of Solar Road Studs must meet the requirements of the actual use environment. The requirement of the Ministry of Transport is from -10 degrees to 50 degrees. The actual environment often exceeds this range, which places higher requirements on the battery.
The design of the circuit board must follow simple and effective design principles, and do not artificially complicate, because one more circuit will increase the possibility of failure. Electronic components must also be carefully selected, because any problem with any electronic component may paralyze the entire system.
Welding must be reliable, because Solar Road Studs bears the rolling and impact of vehicles every day, and a little looseness of the solder joints will cause the line to loosen and fall off. Therefore, when choosing welding torches and soldering tin, you must choose high-quality products to ensure that the solder joints are firm and reliable, and can work in a relatively “bad” environment for a long time.
Solar Road Studs solar panels directly absorb solar energy and convert light energy into electrical energy, which can be said to be the first link in the entire working system of Solar Road Studs; its working efficiency directly determines the working efficiency of Solar Road Studs. Monocrystalline silicon solar panels have been commonly used up to 2014. This is because the photoelectric conversion rate of monocrystalline silicon solar panels is high, about 14%, which can convert solar energy into electricity to the greatest extent to ensure the operation of Solar Road Studs. Time supply of energy. In addition, solar panels must be high-hardness, wear-resistant circuit boards. Solar panels have to withstand the rolling wear of wheels every day. If the strength is not enough, it is easy to wear, which will affect the conversion efficiency of solar panels.
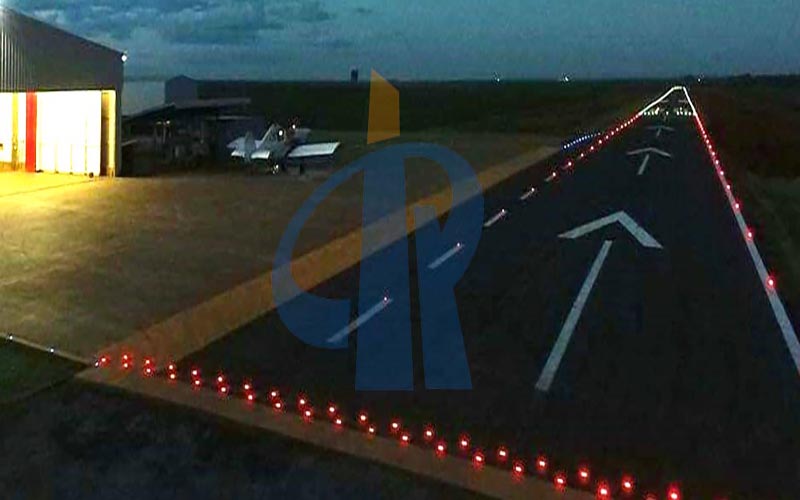
Battery matching performance
Placed for 8 hours under standard test conditions, the rated capacity of the battery should meet the requirements of the road studs for 72 hours of normal light; even if the sun illuminance is less than 1000LX, the battery’s rated capacity should meet the requirements of Road Studs for 12 hours of normal light after 8 hours of charging Needs. This must also be paid special attention. If the battery matching performance is not good, there will be insufficient battery storage power in the rainy weather, causing Solar Road Studs to fail to emit light. In this way, Solar Road Studs has no practical value and cannot be used at all. This is the limitation of capacitive Solar Road Studs. Placed for 8 hours under standard test conditions, the rated capacity of the capacitor can generally only meet the needs of the road stud to emit light for 12-14 hours. Therefore, the capacitive Solar Road Studs has very strict requirements for the actual use environment, not only the sunlight must be enough Strong, and there can be no continuous rainy weather, otherwise it will be difficult to work normally.
Environmental adaptation performance
The use environment of Solar Stud is complex and changeable, and the temperature and humidity may be very different. The temperature in the north is very low in winter, the temperature in the south is very high in summer, the temperature difference between day and night in the northwest is particularly large, the southeast is humid, and the northwest is dry. These will affect whether the solar road stud works normally, so the design of Solar Stud should fully consider the environmental adaptability.
As of 2014, the Ministry of Transportation’s temperature requirements are within the range of -20°C to 85°C, and three cycles of tests between 20°C and 60°C are required to see if it can meet the requirements of the environment. The requirement of the Ministry of Communications for the damp and heat performance of Solar Stud is that it can still work normally after 48 hours of testing under the conditions of 45°C and 98% relative humidity.
The environmental adaptability of Solar Stud is a comprehensive test of its mechanical and electrical properties, involving structural design, circuit design, electronic device performance and other aspects, even including its production process. This also requires all aspects of work to be done in order to ensure that Solar Stud has better environmental adaptability.